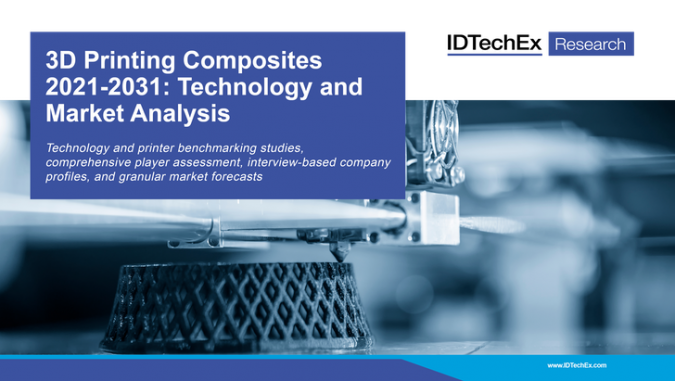
Additive manufacturing of composites is approaching an inflection point. There is an increasing number of printer manufacturers, market launches, more funding, notable partnerships, and importantly demonstratable value-add with a wide range of success stories.
In their new report “3D Printing Composites 2021-2031: Technology and Market Analysis”, IDTechEx forecast the market to reach $2bn by 2031. Although this may not appear like the biggest number this represents significant growth from the current market size; a greater than a 9-fold increase from the calculated 2021 revenue for the most mature extrusion/placement technology is expected. Michael Papish from Markforged stated to IDTechEx that:
“Advanced composite materials opens up new ways to create lighter, stronger parts with less waste in a fraction of the time of traditional manufacturing methods, making them a critical part of an additive manufacturing strategy. We’ve seen demand for new composites and methods grow; in response to customer needs, we’ll launch the FX20 printer later this year, the biggest, fastest and most sophisticated printer we’ve ever developed, which will open up new composite applications in aerospace, defense, automotive and oil & gas.
Over the next 10 years, the global additive market is projected to grow 10x and we believe advanced composite printers and materials will play a key role as manufacturers look for new ways to overcome their supply chain challenges.”
There are numerous main reasons that we are on the cusp of this significant growth:
–Technology maturity. This industry has benefitted from the development of 3D printing polymers and metals, but there are special considerations from the print head through to the software that had to further develop to fully utilize the anisotropic properties from the fibers.
– Application maturity. It takes time for end-users to find the value-add applications and prove out the technology. This has now happened for numerous sectors with benefits ranging from lightweighting through to reducing inventory costs or downtime with replacement tools, jigs, or fixtures. The applications will not be the high-volume end-use parts that grab headlines and that many initially aspire to, but nevertheless, tooling, key roles on the manufacturing floor, and low-mid volume part production are still very profitable fields.
– Supply chain maturity. This is often a challenge for a young industry, but the market has seen key partnerships from material manufacturers to distributors that have helped remove this pain point.
Given this, it is unsurprising that the funding, market launches, and new entrants have dramatically increased in recent years. This competition is healthy, a rising tide lifts all boats, and there are different business models; the only issue may be in IP lawsuits that could slow this growth. There is a significant amount of capital investment in this field and with that IDTechEx are anticipating some M&A activity and, in the longer term, consolidation in the number of players.
The technology progression is also a long way from being complete. There are numerous innovations with some of the most exciting associated with the progression of thermoset resins that will come to market over the decade. Then there is the development of automation within composite manufacturing in general, from simple pick-and-place robots through to rapid preforming.
For more information on this market including interview-based profiles of the main players, technology & material benchmarking studies, granular 10-year market forecasts, and application case-studies, see the market report “3D Printing Composites 2021-2031: Technology and Market Analysis”.