Researchers find a new way of producing industrially important propylene that is more energy efficient than existing approaches—and in the process turns carbon dioxide into another usable resource. Their pioneering catalyst design thus contributes to the carbon neutralization of the petrochemical industry.
Propylene is a gas used to make a large variety of packaging and containers and is considered to be the second most important starting product in petrochemical engineering. However, its production from propane is currently very energy-intensive.
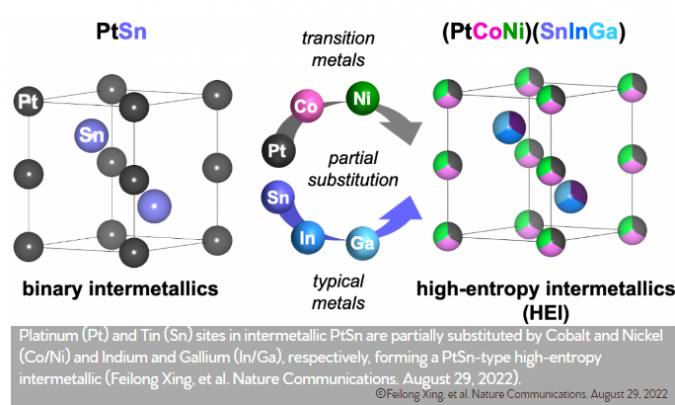
In addition, the process accumulates unwanted side products that need to be purged by burning regularly. It is therefore very desirable to find another approach to the production of this valuable molecule that is more efficient, produces fewer side products, and still uses materials that are stable at high temperatures.
Hokkaido University material chemist Shinya Furukawa and his team recently developed a new catalyst—a substance that acts as a guide to chemical reactions and as such can open up otherwise inaccessible reaction pathways—that allows them to use carbon dioxide to turn propane into propylene instead of the more commonly used oxygen. In their Nature Communications paper, they not only demonstrated that the catalyst was highly efficient, very selective, and stable under high temperatures, but its use also had the side effect of turning carbon dioxide into carbon monoxide, which is a useful resource for the production of many bulk chemicals.
The researchers achieved this feat by building on their previous studies on catalyst design, but this time chose a unique new way: Using an alloy of platinum and tin on ceria support as the base, they replaced a fraction of these atoms with the metals cobalt, nickel, indium, and gallium. Each of these elements was chosen for a specific purpose: Platinum-tin alloys had already been known as good catalysts for the reaction, but including nickel and cobalt increased both the catalyst’s ability to activate carbon dioxide and its selectivity to the desired reaction.
On the other hand, inserting indium and gallium was beneficial for the catalyst’s temperature stability. Finally, the ceria support made carbon dioxide capture and catalyst purging easier. The research team also confirmed that the catalyst can be regenerated and reused without a loss of performance.
Furukawa explains the significance of this result thus: “This work not only demonstrates the outstanding performance of our catalyst, but it also opens up a new window of catalyst design concepts based on our technique. The new catalyst outperforms our previous Pt-Co-In catalyst by a large margin. These insights will contribute to the carbon neutralization of the industrial production of small petrochemicals.”